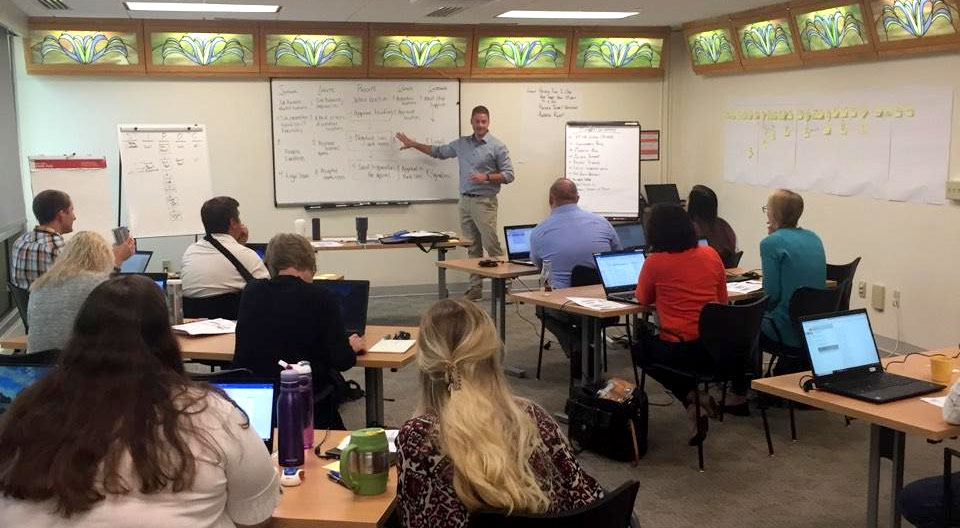
Working to find a solution to the urgent staffing issues so many businesses and organizations are facing
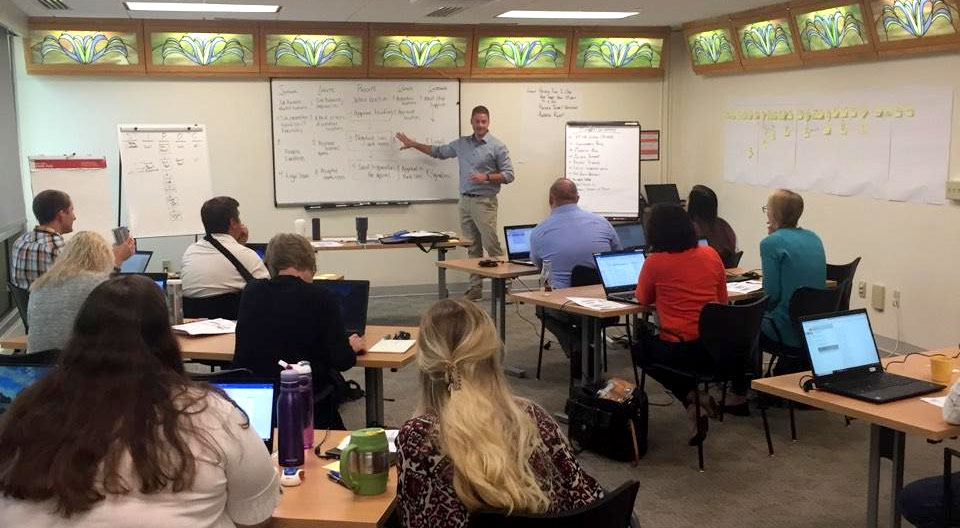
At this point, everyone is well aware of the global staffing shortages and its far-reaching impact in every industry. The fundamental solutions that have resolved staffing issues in the past are no longer working to settle these issues in the current climate. While business forecasters have been tracking this predicament for years, the pandemic has exasperated the issue.
Chris Spranger, executive lecturer in the School of Business and Economics (SBE) at UW-Stevens Point (UWSP) and owner of Spranger Business Solutions, has spent years helping companies and organizations streamline their processes and systems through Lean Six Sigma (L6S). He has been teaching these same skills to students, also known as candidates, in the MBA program.
Starting this fall UWSP will be rolling out L6S certification options. The MBA program will now incorporate the yellow belt certification for all candidates. Also, a green belt certification is available to both students and professionals. The three-class series series can stand alone or be incorporated into the MBA degree.
“With the growing demands on employees, finding ways for them to not only efficiently complete their work but also consistently delivering results to the customers and end users is essential,” said Spranger. “Employee burnout is a real serious issue many companies and organizations are facing today. Lean Six Sigma is a management tool that allows companies to structure the workflow in a way that is manageable for their teams while also continuing to deliver results their external stakeholders expect.”
There are four levels of belt certification in L6S. The first is yellow belt which provides a basic understanding of the L6S concepts. The second is the green belt, which provides the skills to work on process improvements within a company or organization. Third is the black belt which prepares candidates to manage and lead project teams. The fourth and final is the master black belt which provides the skills to train others in L6S along with coaching and consulting.
“Having both of these certifications is a benefit to our local economy,” added Spranger. “Both certificates will prepare achievers to be an integral part of a company or business who is already utilizing L6S. For those who have not yet adapted these skills, having employees who are aware of the systems can be an integral part of laying the groundwork for streamlining processes to match demanding workload so many of our local businesses and organizations are facing.”
Lean Six Sigma is an adaptation of both Six Sigma which was created by Motorola in the 1980s and lean manufacturing which was developed by Toyota in the 1950s. Six Sigma is a set of techniques and tools for process improvement. Lean manufacturing is a methodology that focuses on minimizing waste within systems while maximizing productivity. Lean Six Sigma uses a blend of these systems to create a synergized managerial concept that focuses on improving systems for external and internal stakeholders, making process run smoother with lower risk of error, and maintain consistent product or services to improve the customer experience.
How could L6S help in your career? If you are interested in learning more about the MBA program and the certifications offered through UWSP reach out to the MBA team at mbainfo@uwsp.edu or visit uwsp.edu/mba. Or to learn more about Six Sigma and what it can do for your business or organization reach out to Chris Spranger at cmspranger@sprangerbusinesssolutions.com or check out his website at www.sprangerbusinesssolutions.com.